Experiment: Design and Construction
Idea
What we wanted to analyse is a complex dissipative system consisting of granular material which is driven by some power supplier. In particular we wanted to observe the tendency of such a system to spontaneously form regions of high or low concentration.
Realisation
A simple realisation of this is a transparent perspex box with ping-pong balls (idealised as spherically, uniform particles that dissipate energy under collisions) which are driven by an oscillating bottom plate. If the box is in addition divided into two regions of same size by placing a half-height wall in the middle of the box, one is able to compare the particle densities of two different regions of the system.
The Bottom Plate
The main requirements for the bottom plate were to be light (reduce the required driving power), uniform (reduce its influence on the clustering of the granular material) and non-deformable (avoid self-oscillations at high driving frequencies).
Therefore we decided to use an aluminium frame which is comparably light but yet ensures to remain firm under oscillations. Inside this frame we spanned a net of badminton racket strings which have a vanishing low weight but good reflection properties.
The Engine
The bottom plate should be driven by an engine with variable frequency. A first estimation of the required power yield that we would need a motor power of some kW which is quite a lot. But luckily there was a motor together with a frequency control available at our institute which previously was used to drive a pump but not deployed during our experiments. That one had a power of 5 kW and thus more then actual needed. But we decided to take it nevertheless because it was the by far cheapest solution.
Final Construction
Finally we contacted the central workshop of the faculty in order to ask for support with the final assembly of our experimental set-up. They were willing to help us with that and we discussed the details. Furthermore the workshops of the Max Planck Institute were involved in the construction as well and helped us with the installation of the control electronics. After all the set-up looked like the one in the figure below.
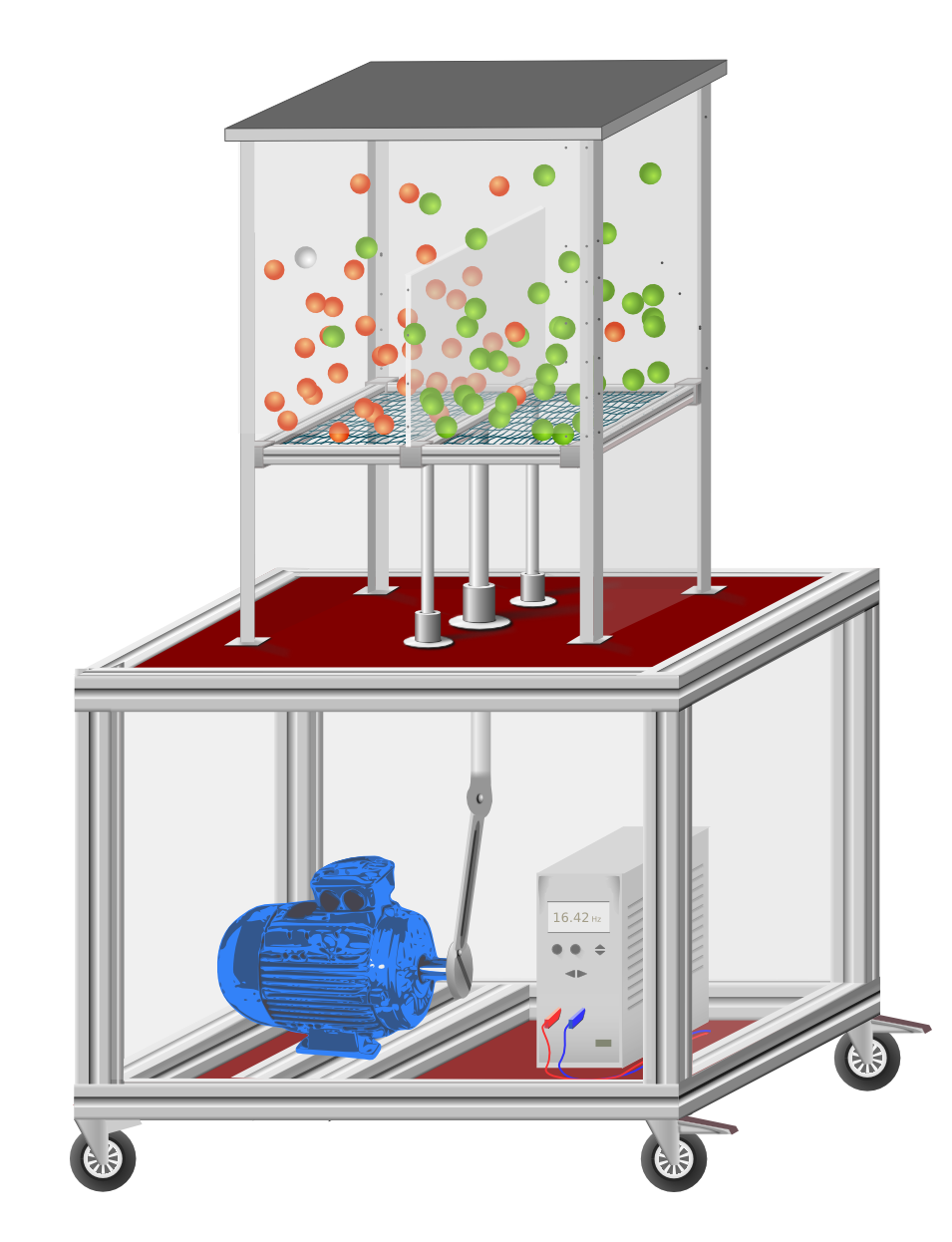
The Measuring Process
What we wanted to analyse in our measurements was the behaviour of this many particle system as a function of various parameter configurations. These parameters were for example the oscillation frequency $f$ of the bottom plate, its amplitude $d$, the number of balls, the height of the mid-wall and of course the time evolution.
However, we decided not to vary the oscillation amplitude $d$ because for large values of $d$ the balls could get jammed between the mid-wall and the bottom plate while the engine is running which would give rise to a considerable damage of the experimental setup. Furthermore there always needs to be a certain safety distance between the bottom plate and the mid-wall which limits the range of possible $d$ values even more. Finally we set its value to $d=0.9$. But luckily this is no big restriction for our experiments since the relevant quantity linked to the amplitude is the bottom plate velocity $v_b$ that can by modified by varying the oscillation frequency just as well.
Since it is not that easy to cover a five dimensional parameter space by measurements, we restricted ourselves initially to measure the dependency on one variable parameter respectively together with the time evolution while the other parameters remain unchanged.
In order to do so we installed a video camera and chose a number of particles that is preferably high but still ensures countability. We intended to let the apparatus run for three minutes for every fixed frequency and take a video of that. Thus we could later evaluate the measurements by taking snapshots of the video every ten or fifteen seconds and counting the particles on either side. This approach would enable us to analyse the time evolution and the frequency dependence of the system at the same time.
Improvement of the Measurement apparatus
However, it turned out that this method was not yet ideal because the fast particles could hardly be detected on the video due to the motion blur, reflections and the bad contrast to the background.
So we did some improvements to the measurement apparatus in order to eliminate these sources of disturbance. For a start we stuck some black paper at the inward of the panels of the perspex box (except for the front window) to reduce reflections and amplify the contrast. Furthermore we decided to take single photos with a reduced exposure time with the camera instead of taking videos so that the motion blur effects are reduced.
Moreover we noticed that the behaviour of the system was dominated by the aluminium frame of the bottom plate because the particles colliding with the frame were pushed considerably harder than those colliding with the strings. So we covered the frame with some kind of rubber to get rather damped collisions here and we raised the tension of the strings to receive better reflection properties.